Why Airlocks?
Ante Rooms Are So Important in GMP Facilities
Airlock systems play an important role in pharmaceutical industries, protecting clean rooms from contaminants, and preventing cross-contamination. As the name indicates, airlocks refer to locking systems utilizing air pressure as a primary mechanism, as a means of protection in cleanrooms against contaminants during human and material movement. An airlock is produced by creating differential pressure between two areas, produced by the HVAC System.
The Design of Airlocks
An airlock is a closed room between two cleanrooms of different classes. Both doors of the airlock should not be opened simultaneously. Interlocking systems should be installed in airlocks to prevent the opening of both doors at the same time, with an alarm system that alerts the simultaneous opening of both doors should it occur. The doors of the airlock should be opened towards the higher-pressure side, so that it can easily be closed by air pressure.
As we know, air moves from an area of higher pressure towards an area of lower pressure. All airlocks work on the same principle; changing the pressure in airlocks or in adjacent areas will produce different types of airlocks.
Types Of Air Locks
There are three types of airlocks:
1. Cascade Airlock
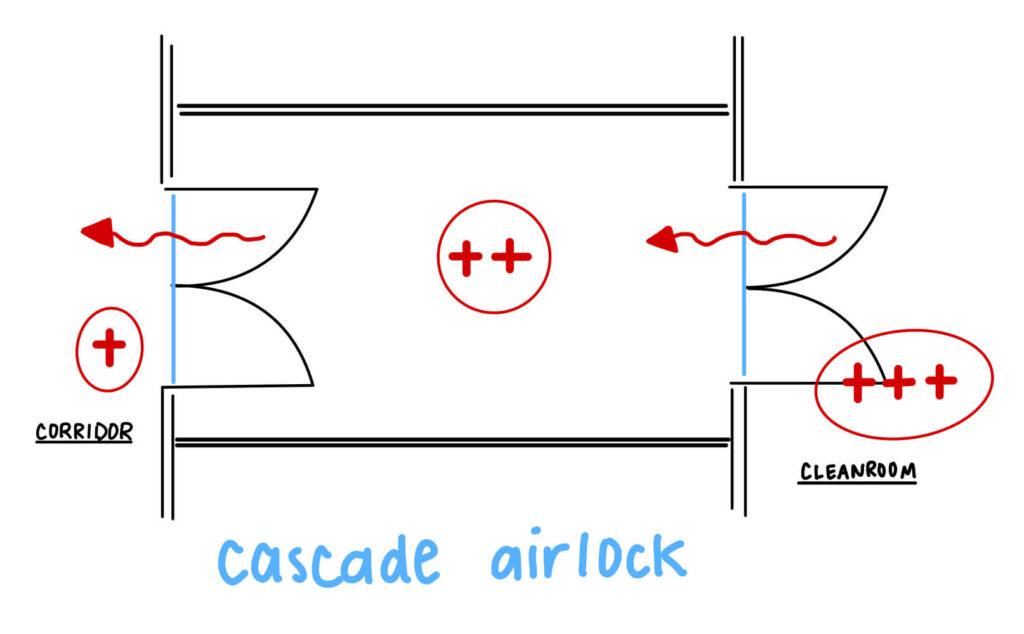
In a cascade air locking system, pressure increases or decreases in ascending or descending order respectively, (from 30 Pa to 20 Pa to 10 Pa \or\ 10 Pa to 20 Pa to 30 Pa). Thus, air moves from higher pressure to lower pressure, preventing cross-contamination. This type of airlock is commonly used in Tablet manufacturing facilities where higher pressure remains in the corridor to keep drugs inside the cubicle.
2. Bubble Airlock
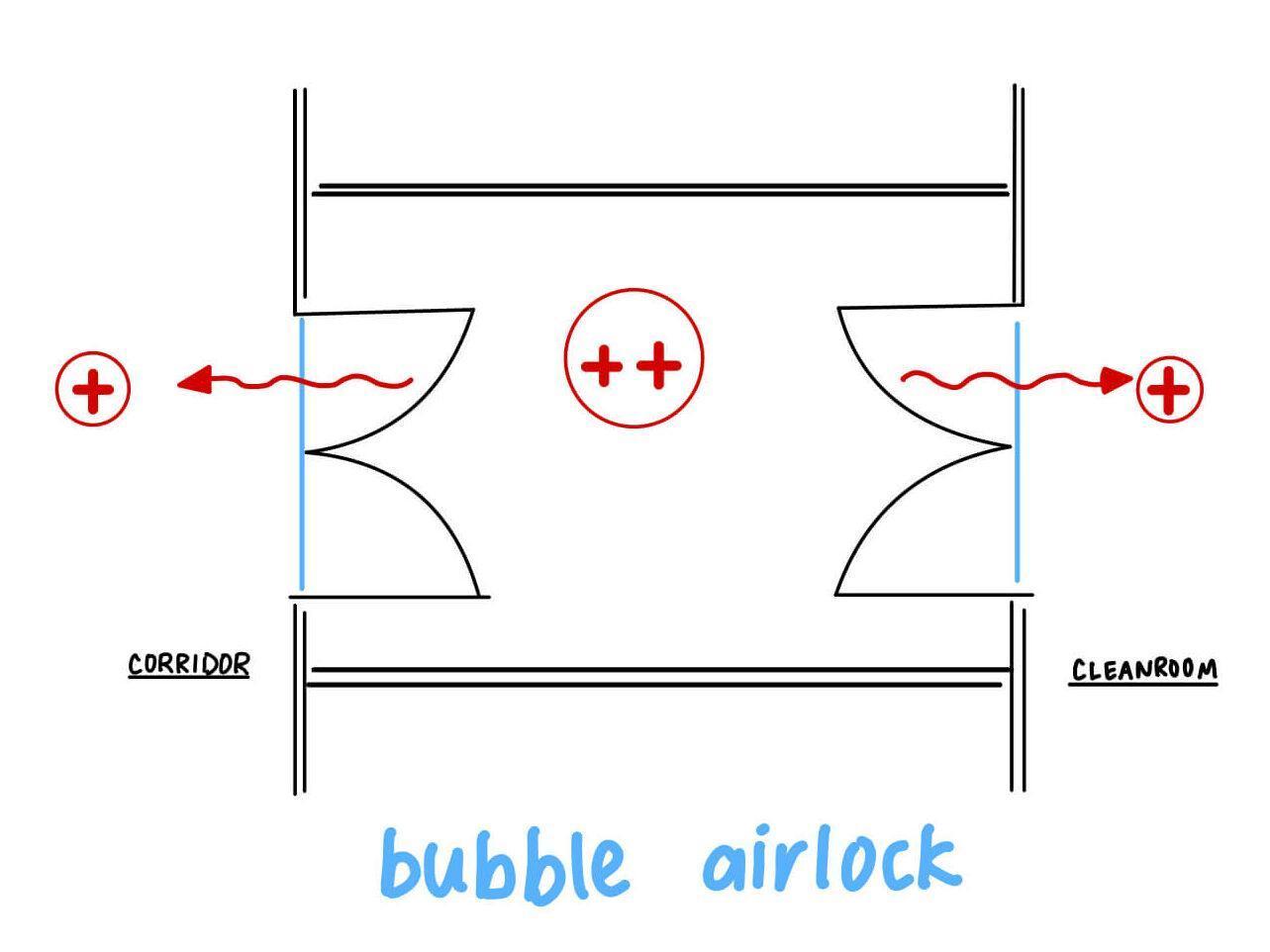
In a bubble airlock, pressure inside the airlock is high or positive, and is low or negative on adjacent sides. Thus, air moves from the airlock to the primary manufacturing area, and in the same way from the airlock to the corridor. Higher air changes are produced in the airlock, thus producing a bubble as it pushes air outside from the airlock. This type of airlocking system is commonly used in Injectable manufacturing facilities so that air contaminants from outside do not contaminate the product.
3. Sink AirLock
In sink airlocks, the pressure inside the airlock is negative, and is positive in adjacent areas, such that the air moves from higher pressure to lower pressure areas. Higher pressure on both sides of the airlock prevents contaminants from escaping the primary manufacturing area. It is commonly used in the manufacturing of harmful substances such as poison.
What Driving Factors to Consider When Designing Airlocks
The effective of an airlock depends on its design, operation, and maintenance.
1. Design
- Airlocks follow the displacement principal. Air will flow from an area of high pressure to an area of low pressure. According to ISO 146644-3 guidelines, differential pressure between adjacent cleanrooms or clean zones typically ranges from 5.0 Pa to 20.0 Pa, which will allow for smooth door opening and closing, and prevent unwanted airflow due to turbulence.
- Doors of the cleanroom should be airtight, so that unwanted infiltration or exfiltration will not change the differential pressure. For achieving a certain pressure inside the airlock, determine the supply or return CFM by adding or removing Leakage CFM.
Leakage CFM = 840 × 2.12 × Door Leak Area (m²) × √ΔP
- Orient doors in a way that they will remain opened or closed due to pressure inside the rooms.
- Airlock doors should have a window panel that provides sight of a person on the other side.
2. Operations
- Both doors of the airlock should not open simultaneously. Simultaneous opening of the airlock doors will result in a loss of differential pressure and invite unwanted airflow.
- Manual or automatic interlocking should be in place to avoid operating both doors simulataneously.
- Install a Magnehelic Gauge or digital display, which can provide accurate information about differential pressure.
- There should be no interference in the closing and opening of the doors.
3. Maintenance
- Schedule airlock inspections to evaluate the effectiveness and operation of the airlock.
- Regular inspections of the bottom seal sweeper, door closers, interlock and Magnehelic gauges is also necessary.
FAQ:
1. What is an Airlock?
An airlock is a small room that acts like a buffer zone between two areas with different
air conditions — such as different pressure or cleanliness. It helps people or materials
move from one area to another without letting the air from one side mix too much with
the other.
2. What should be the size of the airlock?
The size of an airlock depends on the purpose:
- If it’s for personnel: It should be about the size of a small room — around 6 x 6 feet or bigger.
- If it’s for material moving carts or equipment: It should be larger — around 8×10 feet or more.
3. How can you tell if the airlock pressure is correct?
There’s usually a small device near the airlock door called a pressure gauge (like a
speedometer for air). It shows if the air pressure is at the right level.
If the number on the gauge is within the expected range, then everything is working
fine.
If it’s too low or too high, it could mean:
- There’s a leak somewhere
- A door was left open too long
- Or the air system needs fixing
4. What happens if both airlock doors open at the same time?
If both doors open at once, the air pressure can get messed up, letting dirty air into the
clean areas. That’s why airlocks are designed to make sure only one door opens at a
time.
There’s a special system called Interlocking system inside the airlock that keeps one
door closed while the other is open. If both doors do happen to open, it will usually
sound an alarm to let you know.
This keeps everything inside the cleanroom safe and free from contamination.
5. Can airlocks be manually operated?
Yes, you can open and close airlock doors manually, but most airlocks have automatic
systems to make sure they work correctly. These automatic systems help prevent
mistakes and keep the air pressure just right, so everything stays clean and safe.
6. Do airlocks need maintenance?
Yes, airlocks need regular check-ups to make sure they’re doing their job.
Over time, parts like door seals, pressure gauges, and locking systems can wear
out. If they’re not working right, dirty air can sneak into clean areas.
Basic maintenance includes:
- Making sure doors close tightly
- Checking if both doors don’t open at the same time
- Making sure air pressure is right
- Cleaning and checking parts regularly
GET IN TOUCH
Complete the form below to get in touch with our team.