Key Principles of Effective Cleanroom Design
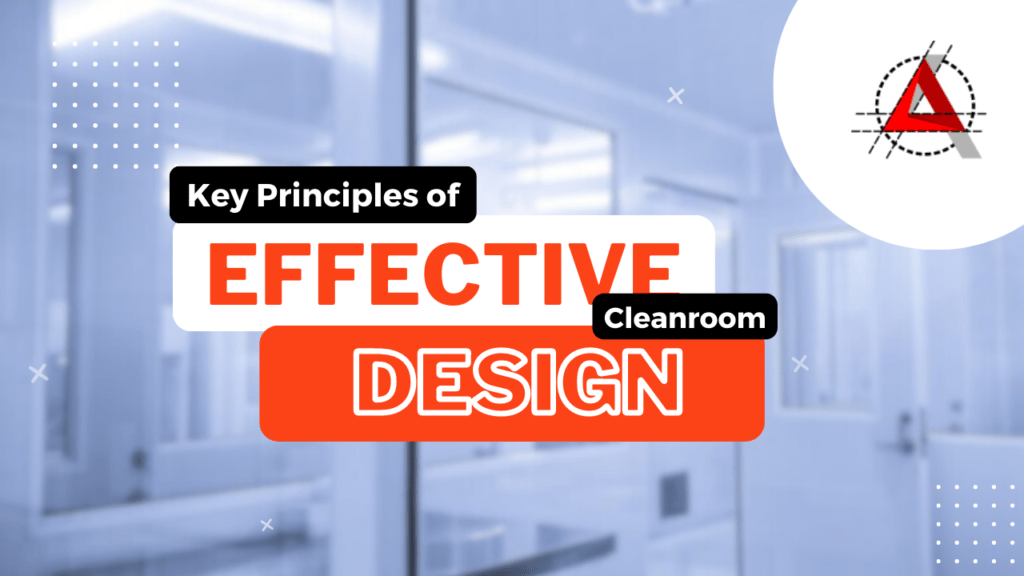
When your objective is to conduct research or manufacture in a space that is as environmentally controlled as possible, it is important to consider key factors in the design and construction of a cleanroom. That means carefully planning for airflow, pressurization, airborne particulates, space temperature, relative humidity and other factors which may impact your required classification of the cleanroom.
Cleanrooms are critical for processes that can range from pharmaceutical production and packaging, medical laboratory and university research, and industrial applications in aerospace, computer components, semiconductors, injection molding, liquid vapes, medical cannabis and many others.
When planning the installation of a cleanroom, there are many critical factors to consider. Let us start with the basics, by looking at what makes a cleanroom “clean.”
It’s all about cleanroom airflow
There are other factors that can negatively impact your work, but the way the quality of the air is controlled is a leading factor determining the success of your space. The main concern is the concentration of particles and microbial contamination in the air. Here are four factors that help define the cleanliness of your cleanroom space.
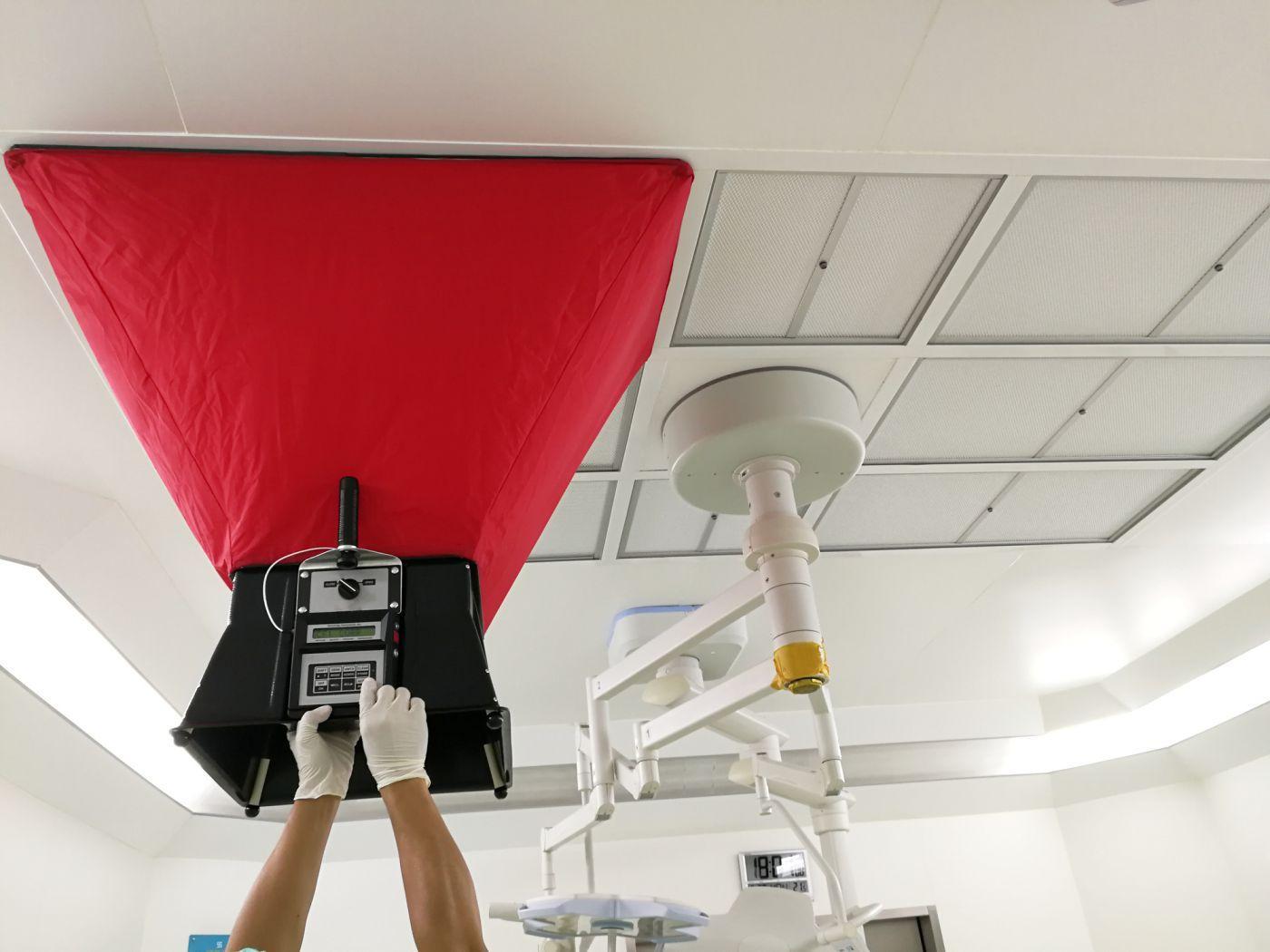
1) Filtration systems
At the heart of most cleanrooms is a highly efficient particulate air (HEPA) filtration system. Spaces in need of even cleaner air might make use of an ultra-low particulate air (ULPA) system.
2) ISO classification
Air cleanliness is rated by ISO 14644-1 Cleanroom Standards. ISO 1-9 classifications grade the quality of the air on the number of particles in the environment of various microscopic sizes. The lower the ISO number, the more sensitive the output and the “cleaner” the room. Typical manufacturing operations are conducted in cleanrooms with ISO 7 or 8 classifications.
3) Air changes per hour (ACH)
Air changes per hour measures the number of times air has passed through the room’s filters. The more pass-throughs, the fewer free-particles will be in the air. ACH is calculated by dividing the volume of air going through HEPA filters by room volume.
An ISO 5 space will circulate some 240 to 360 ACH, while an ISO 8 operation only involves about 10 to 25 ACH. For comparison’s sake, a conventional room or office area will only receive approximately 2 to 4 ACH.
4) Air circulation strategy
Cleanroom air is circulated in one of two ways.
- Recirculating Airflow– Supply clean & conditioned air to the cleanroom space via terminal HEPA filter and return to AHU via return duct.
- Single Pass Airflow – Supply clean & conditioned air to the cleanroom space via terminal HEPA and exhaust it to environment.
There are advantages to both.
Recirculated airflow might be a preferred strategy if your operation is also sensitive to temperature and humidity.
Expelled air from single pass airflow helps reducing micro burden as well as hazardous concentration due to exhaust all air out to environment.
Cleanroom application?
The environmental sensitivity of the work to be performed in the cleanroom will determine the ISO clean air demands.
For instance, the production of medical devices, cell & gene therapy research laboratory and sterile injectable vaccine manufacturing is conducted in cleanrooms with ratings as sensitive as ISO 5 class. Solid dose medicine, Touchscreen membrane assembly takes place in an ISO 7 environment, while general manufacturing processes, nonsterile compounding require only an ISO 8 workspace.
Think about the total layout.
In addition to the cleanroom itself, the surrounding space should also be considered. No matter how well the airflow is controlled, there may be instances of infiltration and exfiltration. There is also air contamination possible through doorways, no matter how the cleanroom is designed. In fact, one important design consideration is a single doorway, minimizing air loss through this architectural feature.
The surrounding space very important. Cleanrooms should be laid out so there is no more than a two-magnitude rating difference between adjoining cleanrooms. As an example, an ISO 5 space can be next to an ISO 7 room but should not directly adjoin an ISO 8 cleanroom.
Watch how air infiltrates and leaks from your space.
Air will infiltrate (enter) and exfiltrate (leave) the cleanroom, sometimes in unplanned and unanticipated ways. The objective is to control the rate at which both occur. Air leakage should be controlled at a rate of 1-2%.
The rate of air filtration from outside can be controlled by adjusting the air pressure within. Positive air pressure will keep “dirty” air from adjoining spaces and prevent it from entering the cleanroom. By having a pressure differential of 0.02 to 0.05 water gauge between the space and the dirtier environment, contaminant infiltration risk is greatly reduced.
It is important keep architectural air exit points to a minimum. Exfiltration will happen through the room’s light fixtures and electrical outlets, door, and window frames and where walls meet floors and ceiling. These are important to consider when designing a cleanroom space.
Construction materials.
When building a cleanroom space, it is important to use materials that will not shed, generate particulates, create space for micro-organism placement or produce static electricity. Surfaces should also be suitable for easy cleaning. The best smooth and easy-wipe materials include HPL, Powder coated GI, glass, stainless steel, and others are the best cleanroom material.
Material quality, strength, modularity, and durability are other factors to consider when reducing leakage and maintenance.
Modular Cleanroom walls, Ceiling, Doors, Windows can be made with the concept of GMP (Good Manufacturing Practice) principles.
Employees are contaminators too.
Consider workflow as well as airflow. It is estimated that as much as 80 percent of cleanroom contamination is due to workers in the cleanroom space.
Reduce contamination by having single-access doorways and pathways. Building a controlled environment space that is big enough to accommodate your needs is also important. Consider the number of workers, the work they will be doing, how that work will flow and even the entry and exit points for materials. To maintain the cleanroom state, it is important to design the optimum personal and material flow which can reduce the cross contamination. Many companies design the facility which has one way flow pattern, separate entry and exit points and appropriate gowning procedures.
Pending on your application, and work processes there might be many other factors to consider.
Protrusions.
What is protruding into the cleanroom – are they disrupting any surface? During design & construction, eliminate as many as you can. Common offenders include:
- Lights
- Smoke detectors
- Power points
- Sprinklers
- Fire doors
Power Supply & Lighting.
- Know where/ how the equipment is to be located, then coordinate the location of the power points/ MCC.
- Power outlets should be recessed on wall (slim design type), no sharp edges. Make sure no exposed services/ cabling will appear in the cleanroom.
- How will it be serviced? Can this be done from outside the room, or will you need to shut down the room to replace a light fitting? Use sealed IP65 lighting types, with top maintenance access. LED lighting types are preferable.
- Ensure there is adequate lighting levels for the required tasks, i.e., 400 lux as recommended in AS/NZS 1680. Also, ensure lighting uniformity.
- Do any specific tasks that need higher lighting levels? e.g., in precision tooling, inspection etc.
- Lighting control modules should be located outside the clean room.
- Provide emergency and exit lighting to current building code requirements.
Viewing Windows – Corridors.
- Have you got enough viewing windows into the clean room so that supervisor / visitor can walk through without going inside the cleanroom?
- Consider double glazing if you have a window between two sterile areas – this will allow the glass panes to be flush with the wall (no sill), making cleaning easier.
- Airlocks
- Consideration should be taken to have personal & material airlocks. Pending on application, those can be separate or combined.
- Personal airlock is used for gowning and degrowing procedure to enter cleanroom from non GMP area.
FAQs.
Q: What are the recommended guidelines for Cleanroom Design & Construction?
ISO 14644-4:2001 – Cleanroom Design, Construction & Startup
Q: What are the ISO classifications for cleanrooms & how are they defined?
Clean rooms are classified by how clean the air is. Developing an ISO Clean Room is an advanced process that measures the airs quality. Within our cleanroom design and construction process this is important in defining the quality of clean are in an ISO Clean room and various clean room designs that our company manufactures.
The Air Change Per Hour is also an important criterion that needs to be met in order to be certified as a ISO cleanroom. Below are the FS209E classifications for Air Change Rate:
Q: Reference for cleanroom certification?
Cleanroom Certification test is recommended to be performed according to FS 209E and ISO 14644 classifications guideline and IEST-RP-CC006.3 standard.
Q: What are the various cleanroom construction methodologies?
- Conventional Construction – Drywall with epoxy paint
- Modular Construction – HPL, GI, Aluminum insulated prefab panels.
- Cladding over existing structure – FRP, PVC, Aluminum sheet
Q:- What is the allowable particulates in each ISO classification?
Below is a table for the ISO 14664-1 cleanroom systems standards.
GET IN TOUCH
Complete the form below to get in touch with our team.