What to Look for in Cleanroom Laboratory Furniture
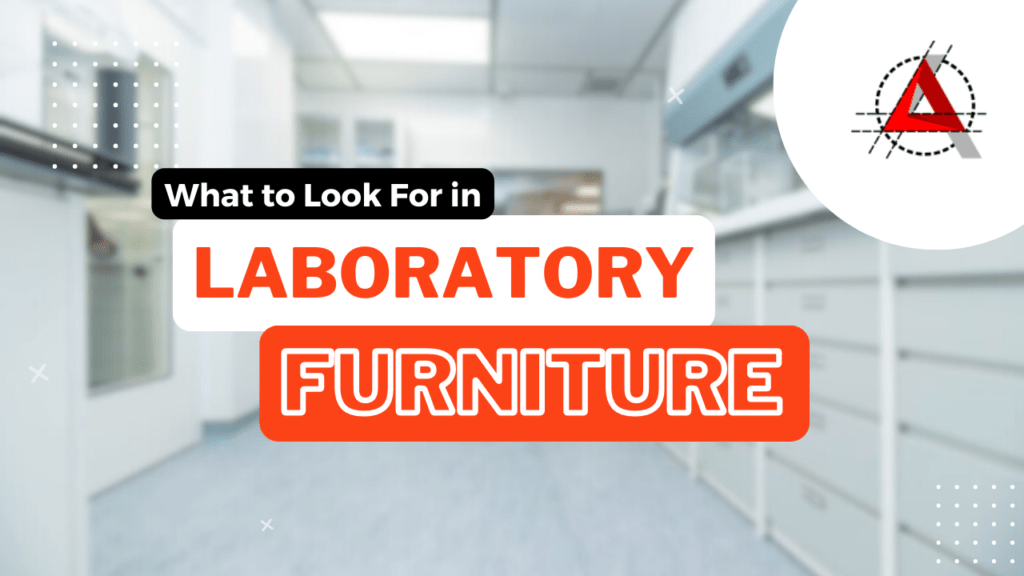
The subtleties of cleanroom laboratory furniture are of the utmost importance. The chairs, stools, tables, and other furniture used in regular work settings, homes and other spaces are not ideal for cleanrooms. Cleanrooms are sanitized, clean and protected spaces that require specialized furniture. The best cleanroom furniture has the fewest possible opportunities for deposits. This means it is well-constructed to the point that it does not allow particles to move below the surface or linger on the surface and compromise the integrity of the cleanroom. Ideally, the cleanroom furniture will be comprised of antistatic materials, meaning it dampens or decreases electrostatic discharges. The buildup and subsequent discharge of static electricity has the potential to significantly damage electrical components. Let’s take a closer look at the top considerations when selecting cleanroom materials.
Mind the Surfaces
The surface of furniture used for seating should be resistant to abrasion. This means cleanroom furniture should not be comprised of fabric. Cleanroom tables, transport trolleys and additional furniture used for storage should have a melamine coating. Stainless steel and additional plastics are also sufficient. Ideally, the entirety of the upholstery in the cleanroom should be covered with plastic so contaminants cannot settle on the furniture. GMP (Good Manufacturing Practices) compliance is also important in the context of cleanroom laboratory furniture. GMP guidelines mandate that cleanroom furniture surfaces should not generate particles or permit the accumulation of dust, in addition to being strong to the point that it endures hard cleaning chemicals without rusting.
Comfort Matters When Selecting Cleanroom Laboratory Furniture
The quality of the chairs used in your cleanroom is particularly important. Aside from featuring a non-porous surface, seating should also be height adjustable to ensure several employees can sit side-by-side while using a single workbench. In short, cleanroom chairs should be the perfect unison between comfort and flexibility along with material that does not absorb particles. If the cleanroom employees prefer to stand while working, consider providing them with standing aids.
Chairs as Cleanroom Laboratory Furniture
R&D centers, laboratories, and other cleanroom employees need and deserve comfortable seating, considering they will be spending hours sitting in the cleanroom. Ideally, the space will have both regular chairs and stools so staff members can alternate between the two as desired. However, selecting any old chair will not suffice. Furthermore, chairs with varying heights should be in the room, so both short and tall technicians have a comfortable place to sit. If investing in several chairs and stools of varying heights will prove too costly, the chairs you select should have flexible heights that cleanroom staff members can adjust as desired. Keep in mind, it is possible for the cleanroom chair to prove non-compliant. The typical cleanroom chair has five legs, is built with aluminum or tubular steel, and has a reinforced plastic base.
Stools as Cleanroom Laboratory Furniture
If you are questioning why some cleanrooms have stools, consider the fact that these seats are backless, creating less of a chance that particles will be generated or stick to the chair and compromise the integrity of work conducted in the cleanroom. Alternatively, chairs have backs and armrests, meaning the garments worn by cleanroom staff will press and rub against them, transferring particles. The only downside to using stools is they have the potential to prove quite uncomfortable after an extended period of use. If stools are used in the cleanroom, they should have glides at the workstations that require minimal movement or at least be positioned in parts of the room that do not mandate the user be seated for several hours in a row. However, as long as the stool is complete with casters, it will prove quite helpful for shifting from one workstation to the next.
Cleanroom Drawers
Drawers below the countertop should be easy to operate. Ideally, cleanroom drawers below countertops will be designed without handles. Handles are surfaces that several people touch, meaning they heighten the chances for contamination. The countertop should be chemical resistant. Ideally, the counter will be Trespa. Trespa TopLab products are perfectly suited for cleanrooms and other laboratory environments that have high standards for sanitation and cleanliness. Trespa materials provide 24-hour chemical resistance, prevent bacterial growth, prove resistant to wear and scratching, are easy to clean and impact resistant. Furthermore, the best cleanroom furniture is flexible, modular, and ready for use upon delivery. This is exactly what we provide for each one of our clients.
Cleanroom Laboratory Furniture Should Use Vinyl or Polyurethane Instead of Cloth
It is a mistake to add upholstery made of cloth to your cleanroom. Rather, the seating should be comprised of either polyurethane or vinyl. Cloth upholstery is problematic as it generates particulates. The benefit of vinyl and polyurethane is cushions made with such material are full of foam and properly sealed to stop particulates from moving into the cleanroom. Air moves out of such a seat as soon as the technician sits in the chair, reducing the chances of particulates lingering in the space. Furthermore, vinyl and polyurethane are that much easier to clean.
Recognize the Merits of Stainless Steel
The materials used for cleanroom tables and other supporting surfaces that facilitate the completion of work are also of the utmost importance. Ideally, these surfaces will be comprised of stainless steel. The advantage of stainless steel is that it does not rust and can withstand heavy and rigorous cleaning. From cupboards to tables and other surfaces, stainless steel is the optimal material for cleanrooms. This material can be electropolished with either sliding or hinged doors. Furthermore, it is also quite easy to add internal shelves with perforated or solid options if desired.
Frequently Asked Questions
Why is modular furniture important for cleanrooms?
Modular furniture is essential for cleanrooms as this furniture qualifies as pharmaceutical grade. The best furniture designs and installations are focused on safety, storage and convenience that ultimately boosts cleanliness and efficiency. Furthermore, a nuanced press fitting system is used for optimal sealing to facilitate module interchanges. Our team is the industry leader in this specialty.
What features should I look for in cleanroom laboratory furniture?
The best cleanroom furniture makes it easy for technicians to reach the items they need in a timely and seamless manner. Furthermore, the surfaces should be smooth for easy maintenance and cleaning. Ideally, furniture pieces will be easily relocated, interchangeable and easy to install.
Why is it important that no welding is done?
Cleanroom furniture processed with CNC Machines is made with a unique press fit that ensures welding is unnecessary, ultimately guaranteeing that no gaps form. Preventing such gaps is essential for the prevention of bacteria growth and other potential forms of contamination.
GET IN TOUCH
Complete the form below to get in touch with our team.